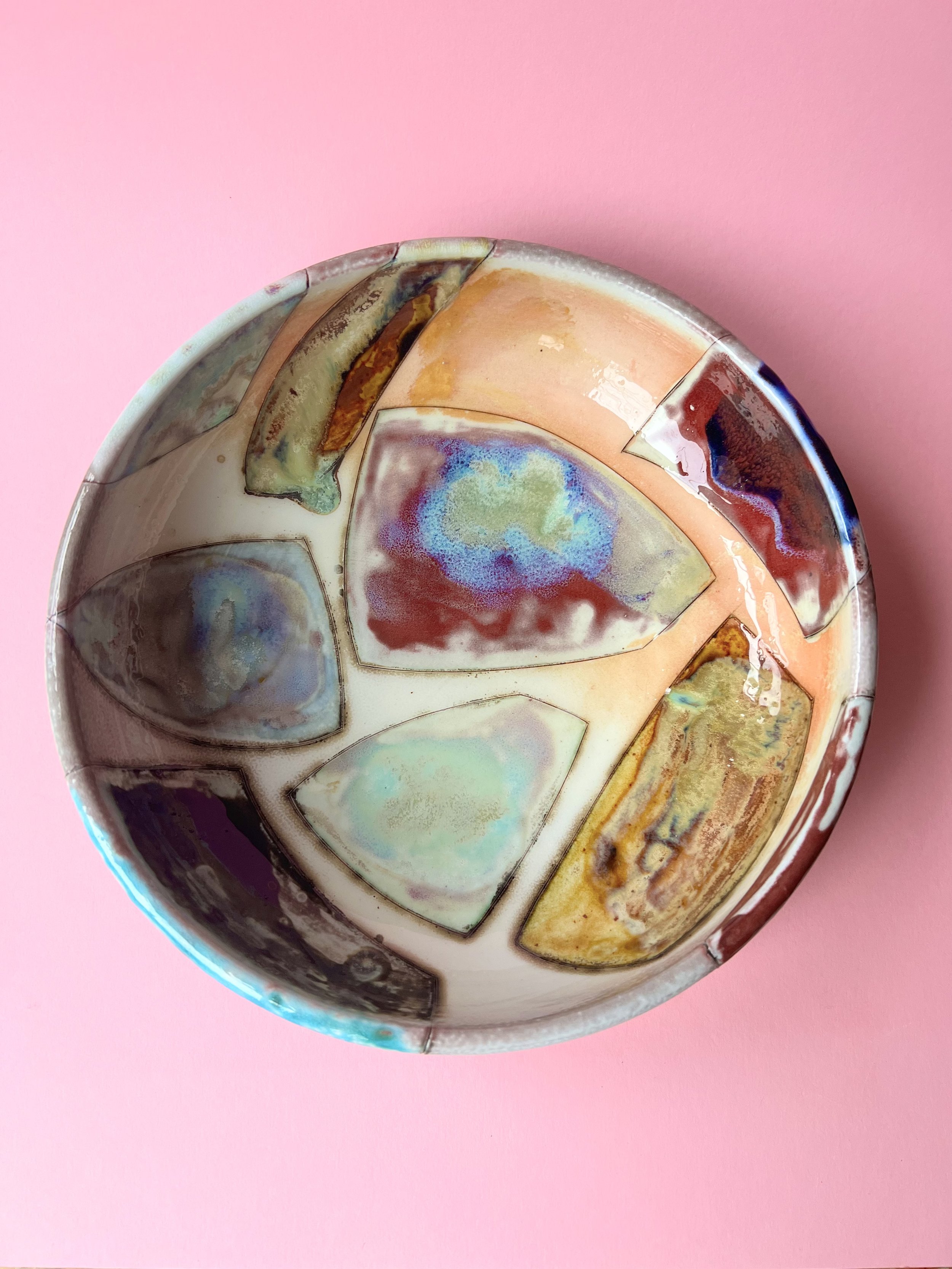
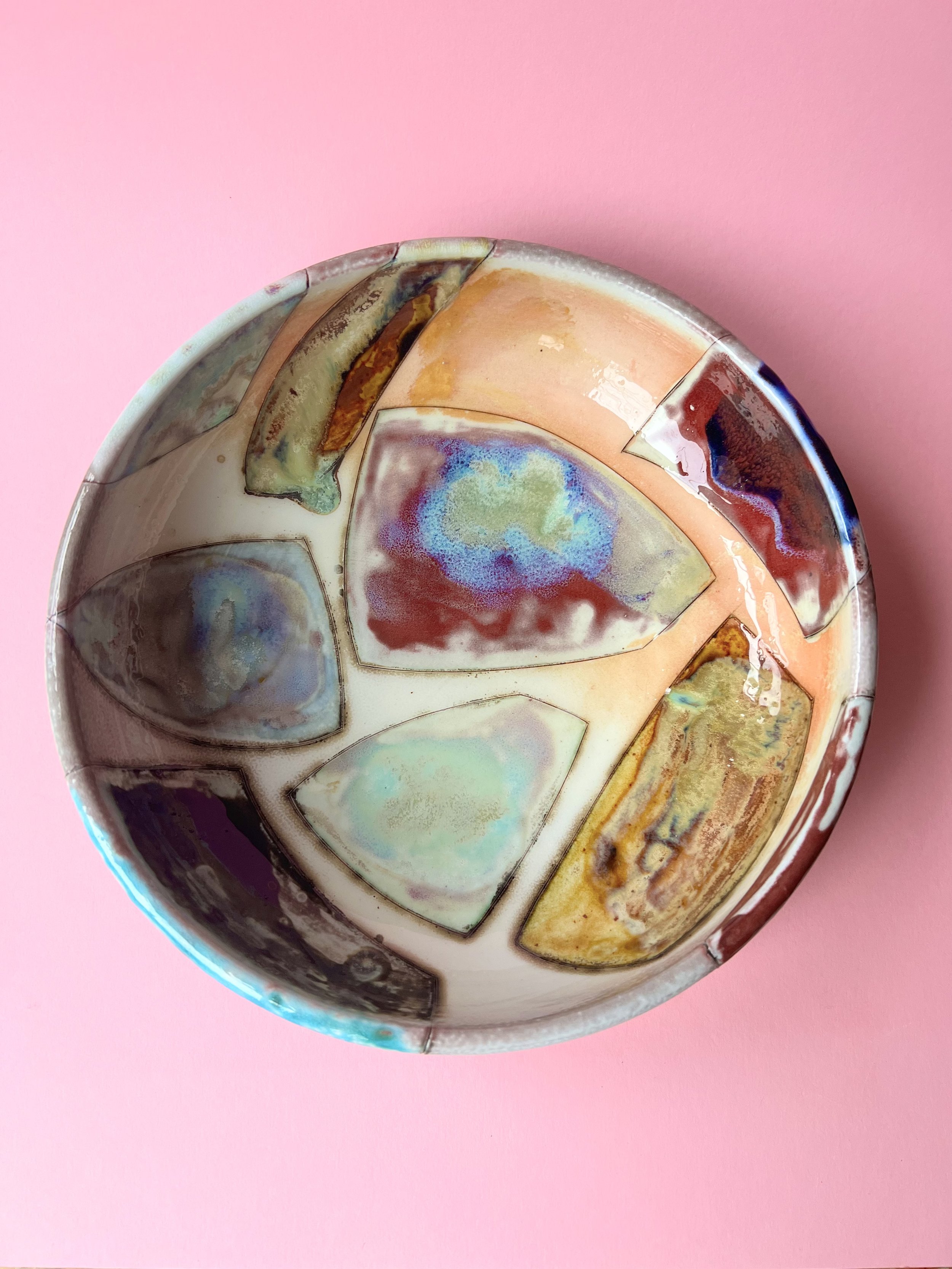
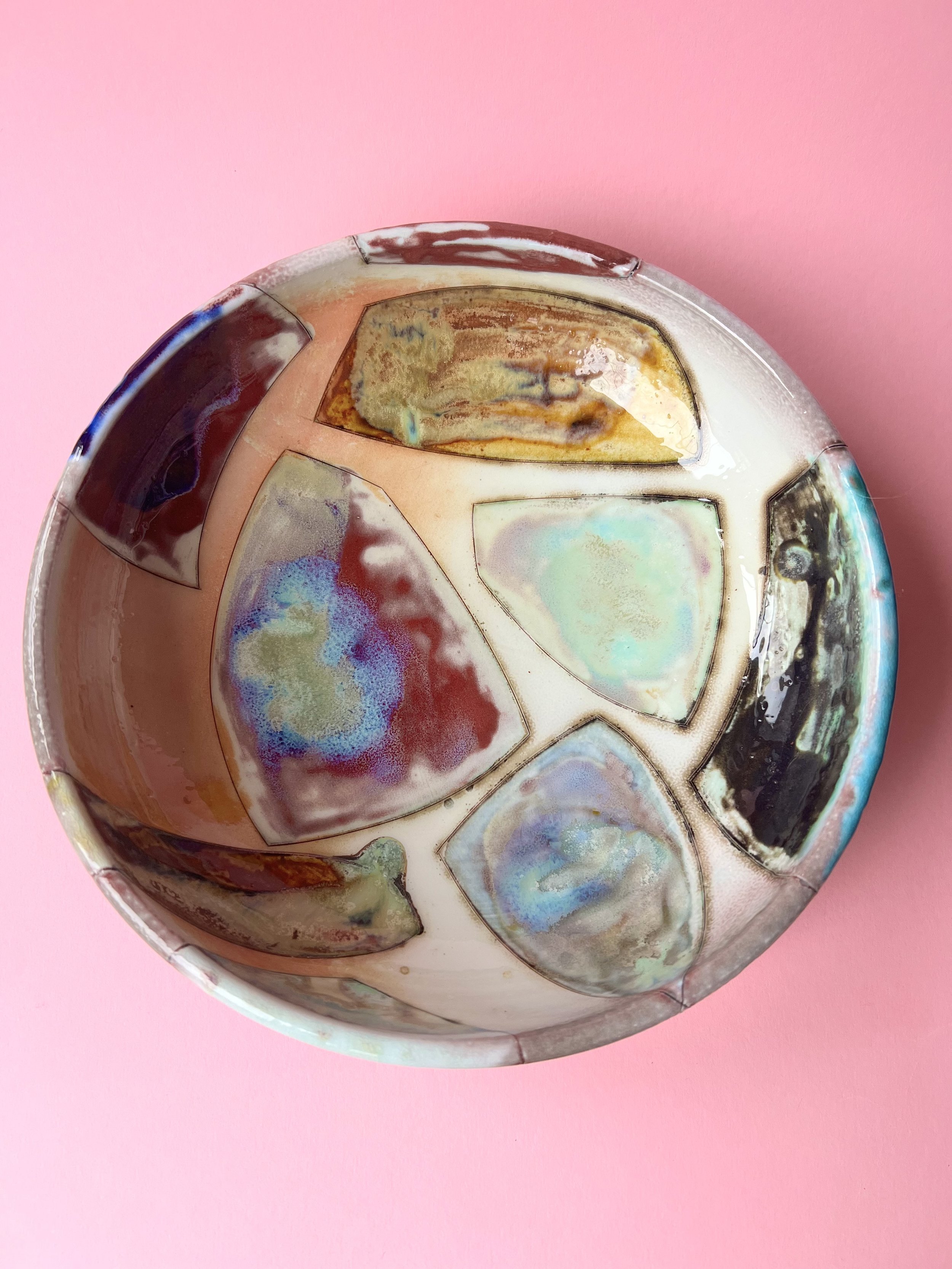
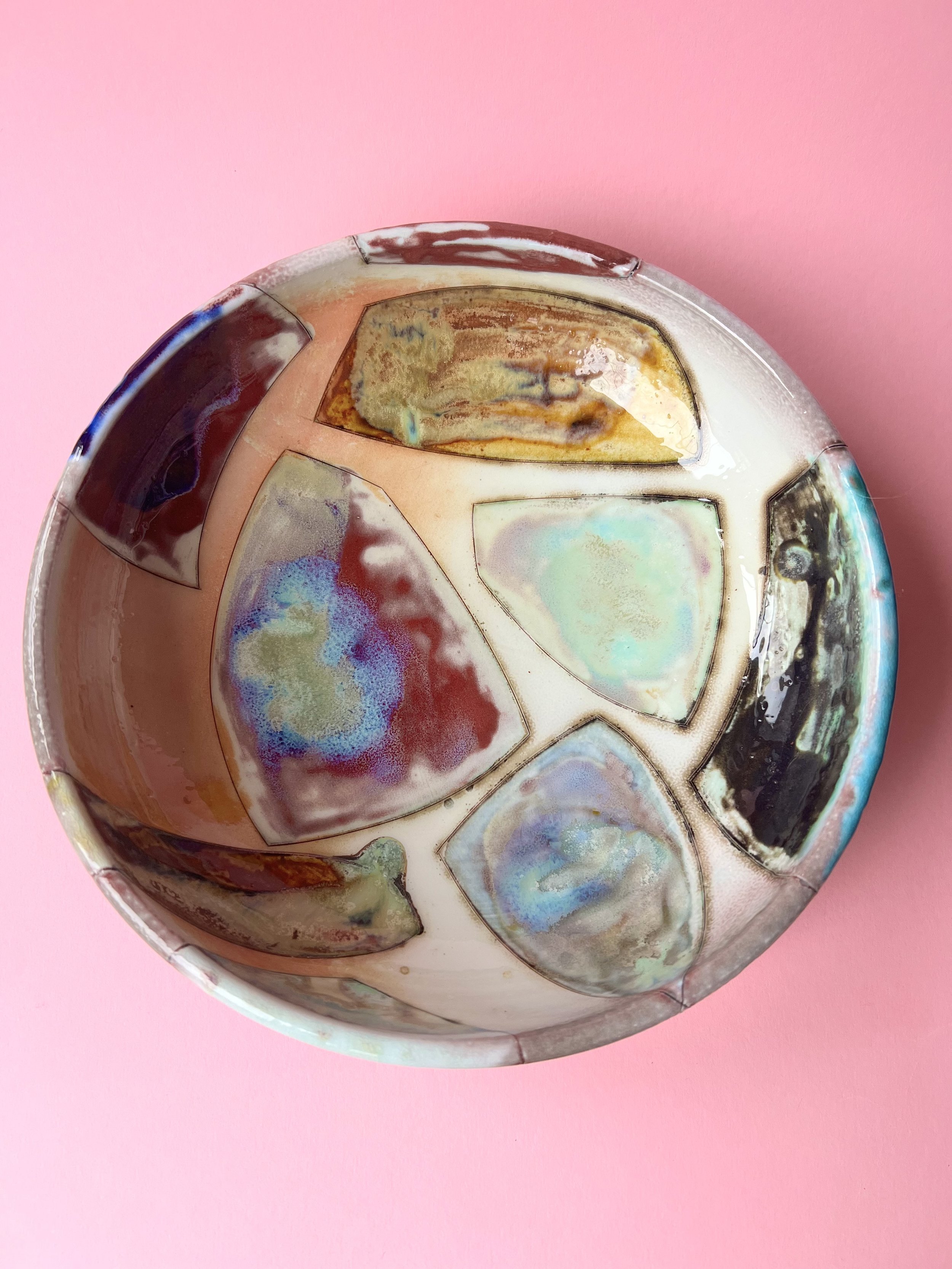
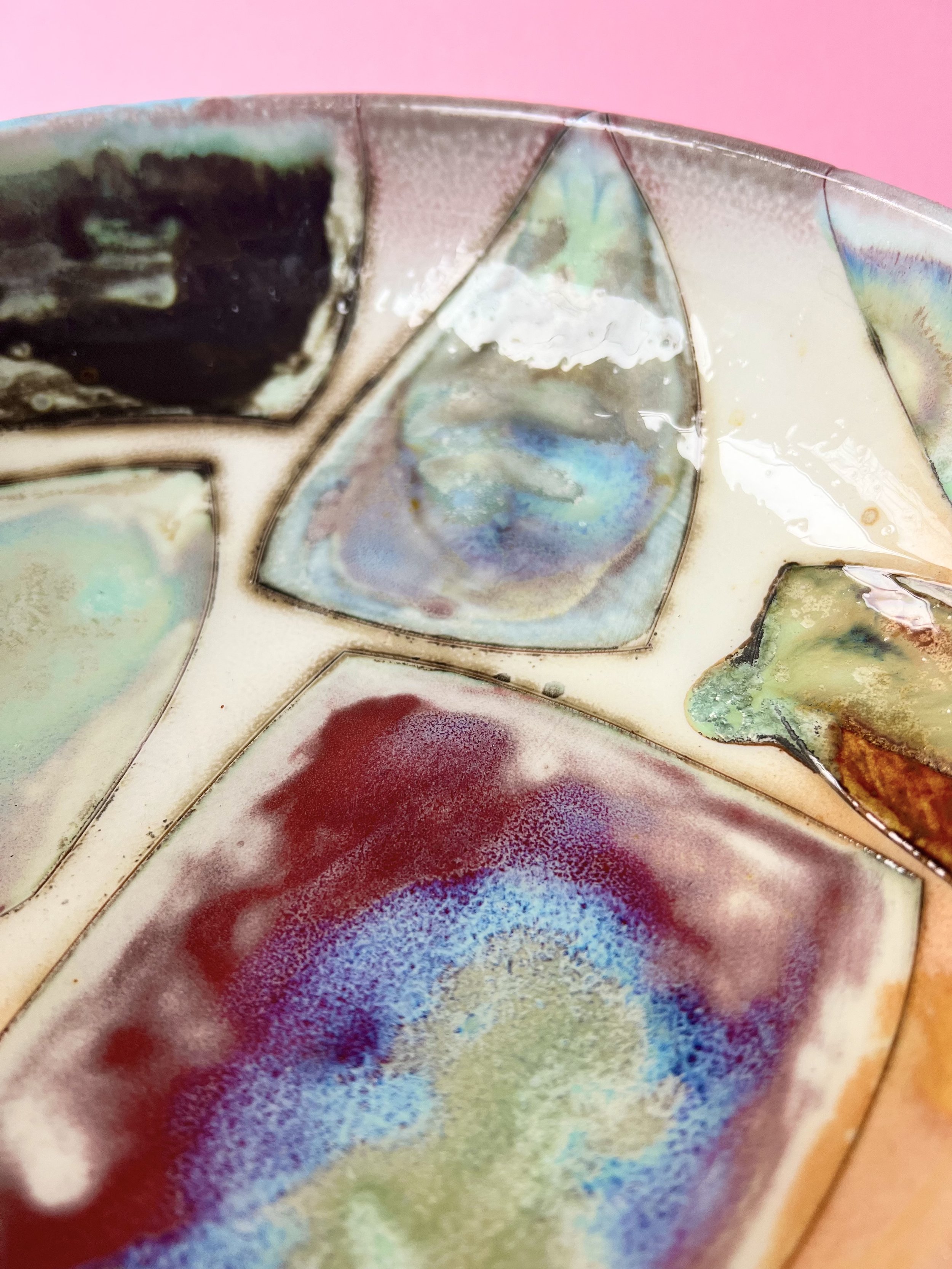
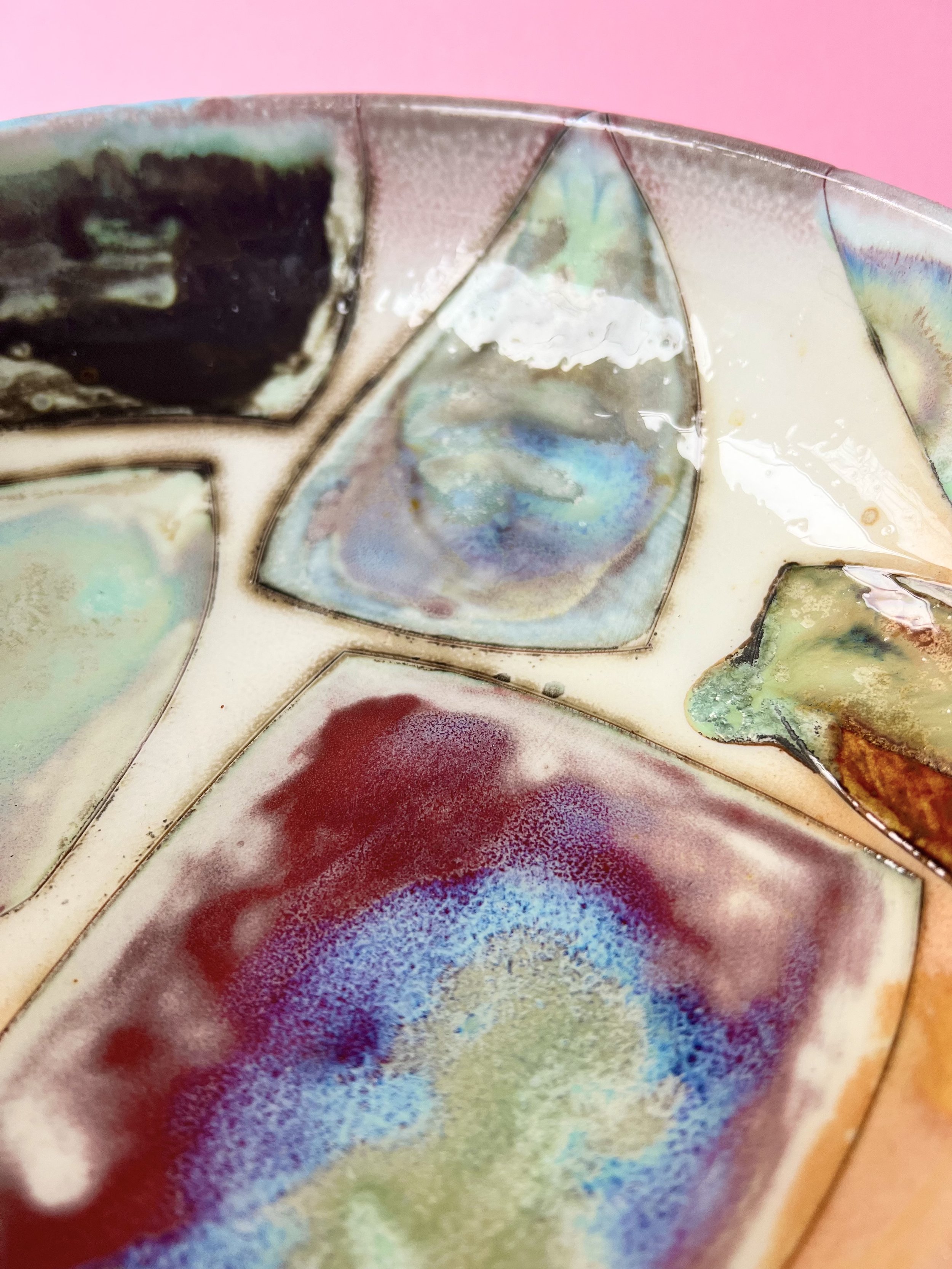
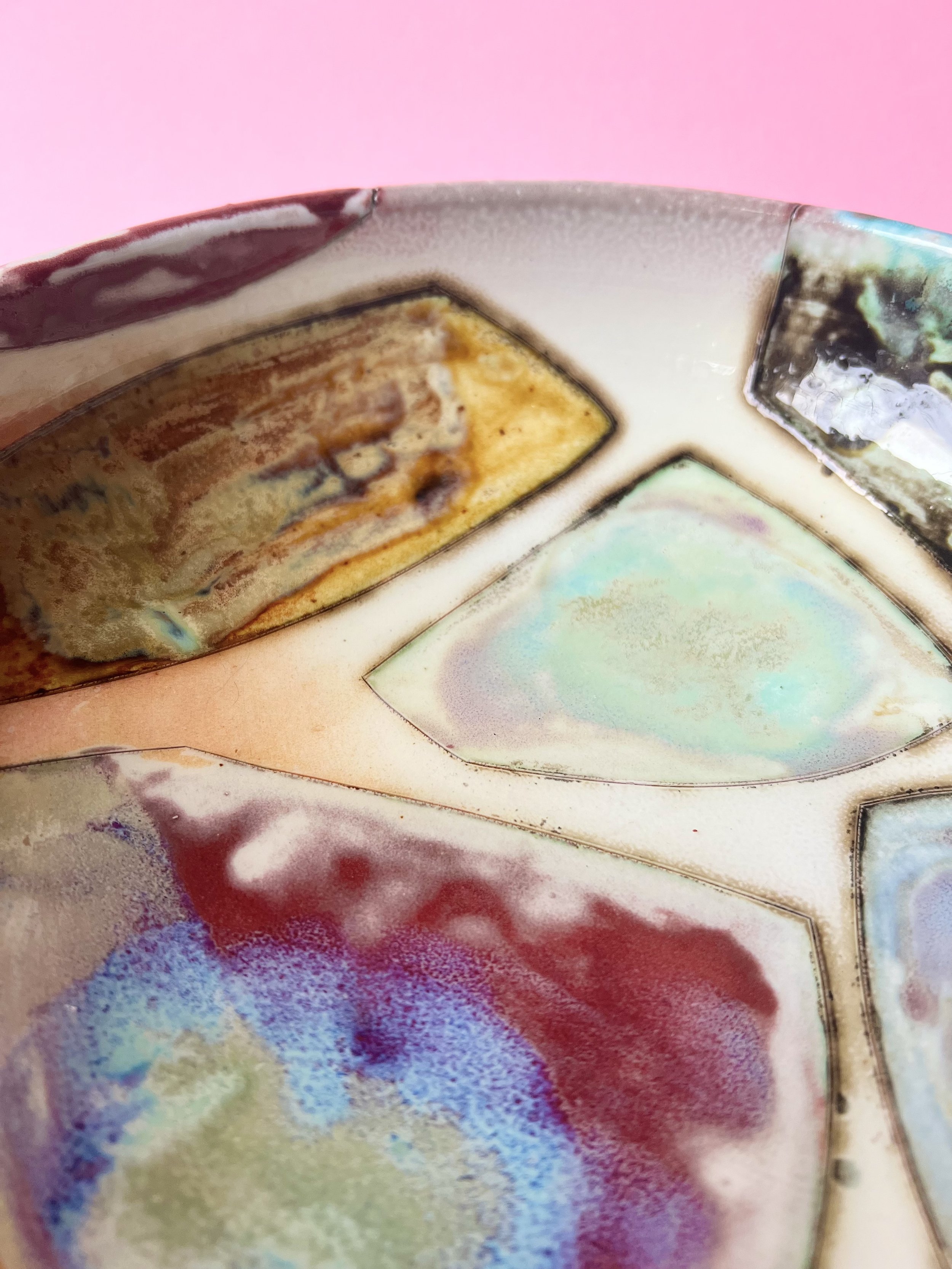
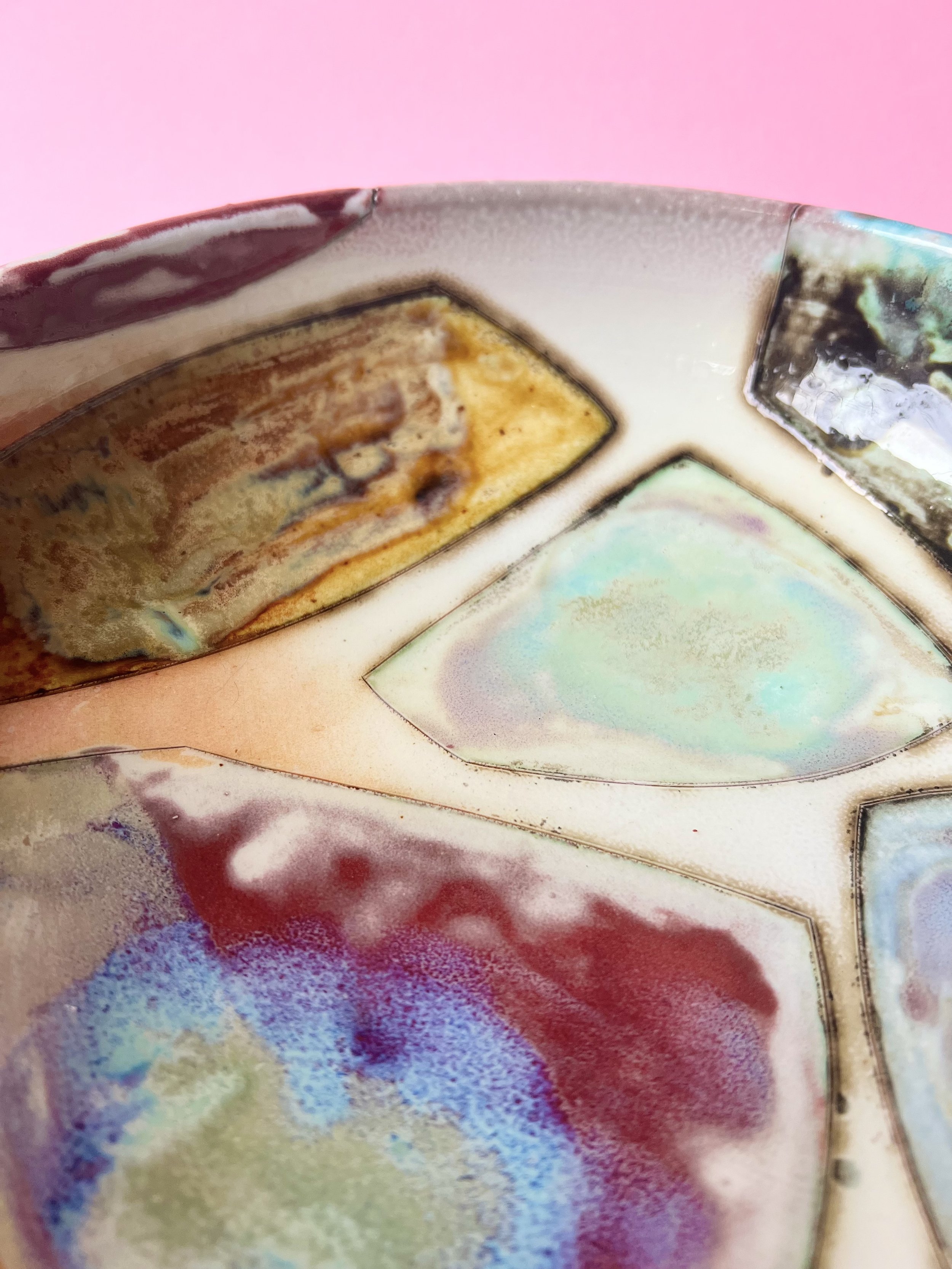
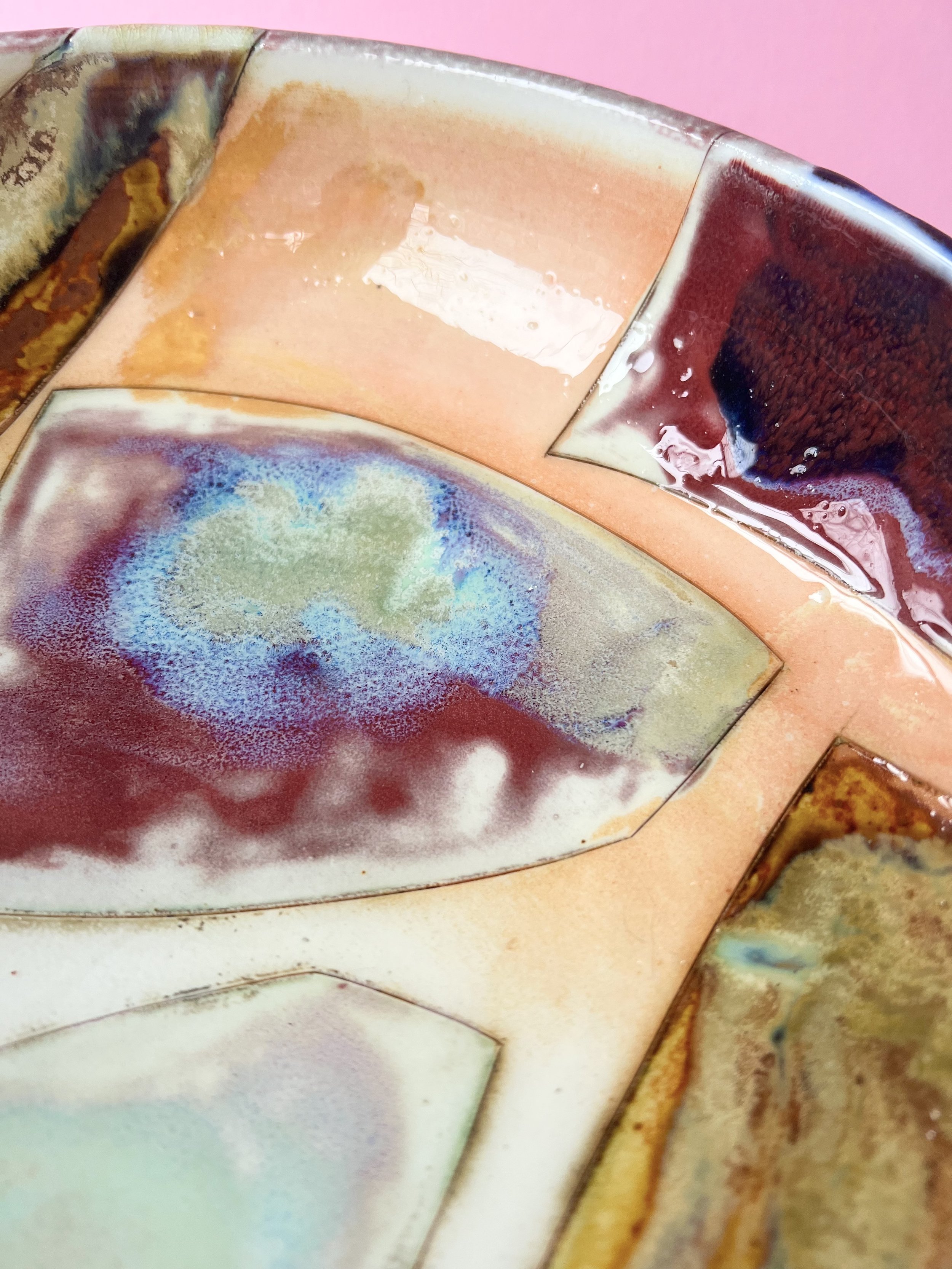
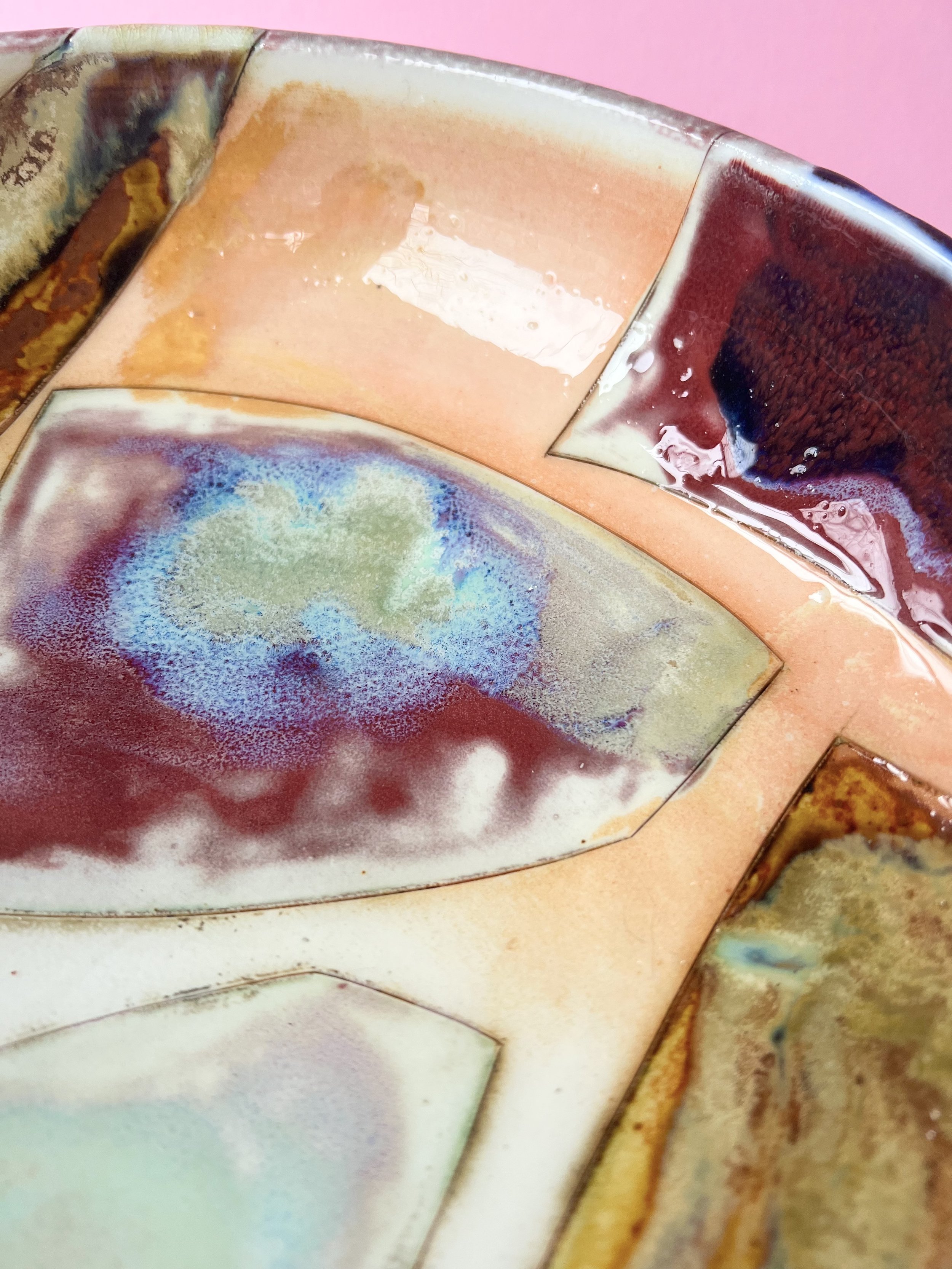
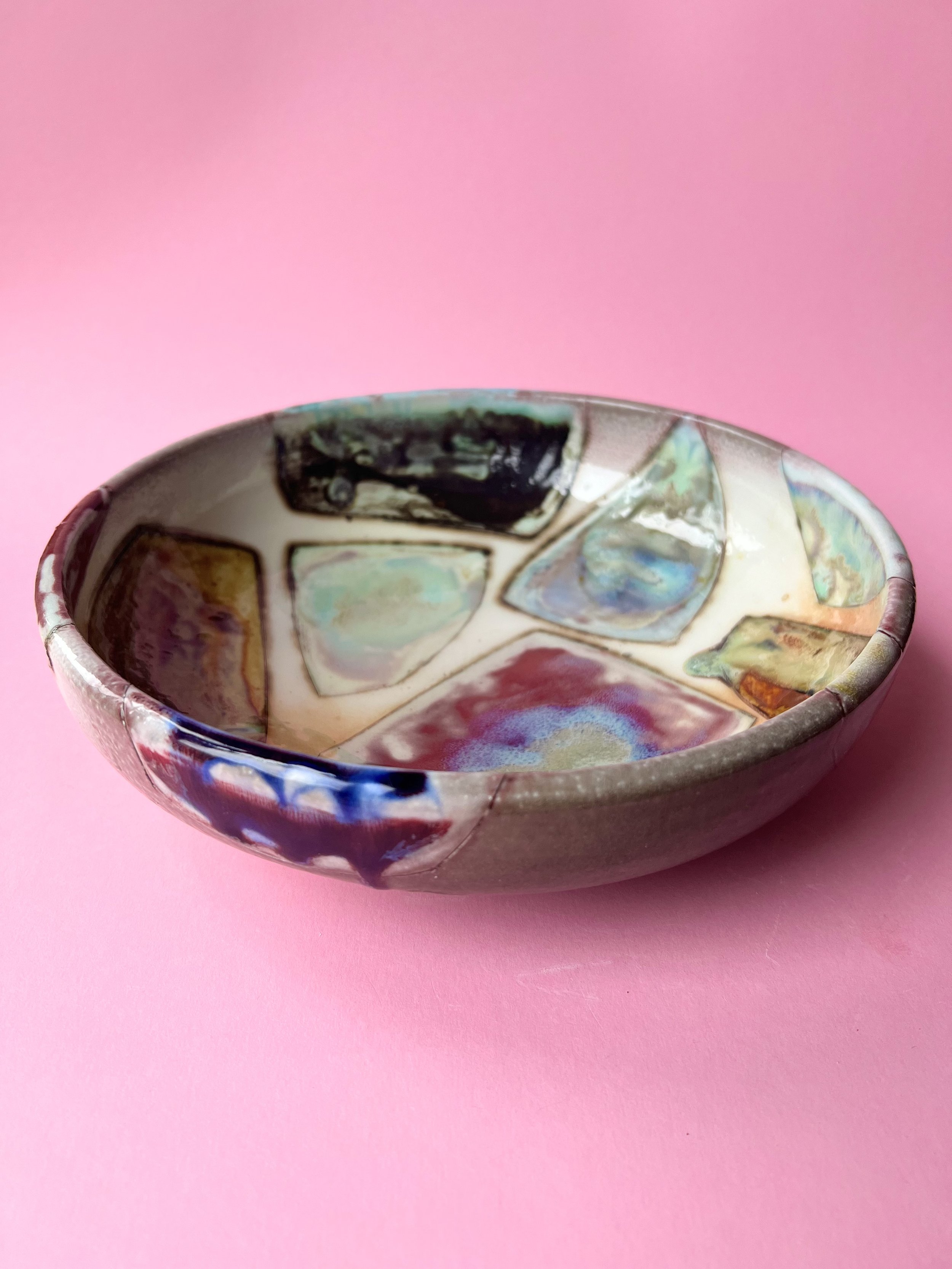
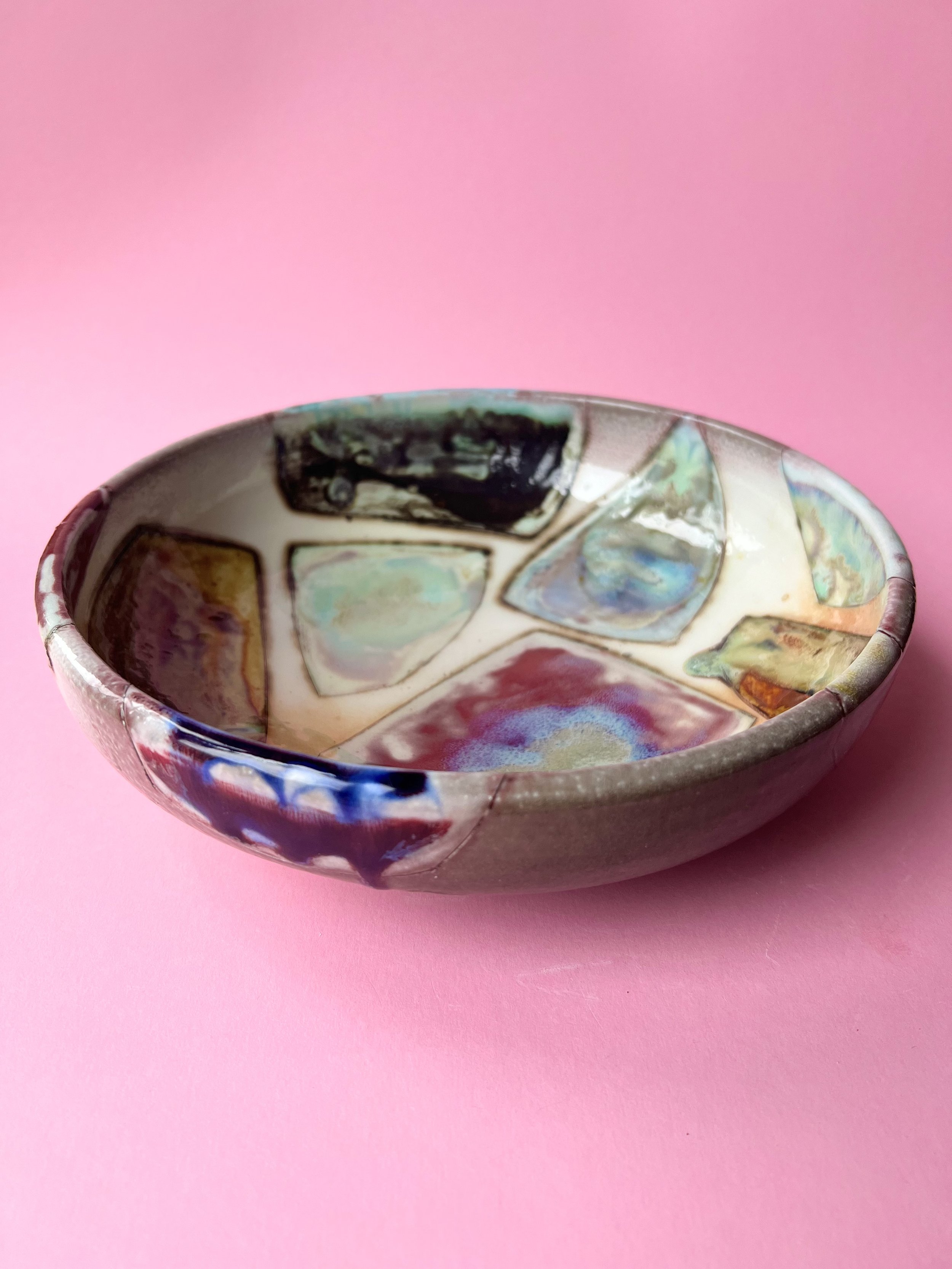
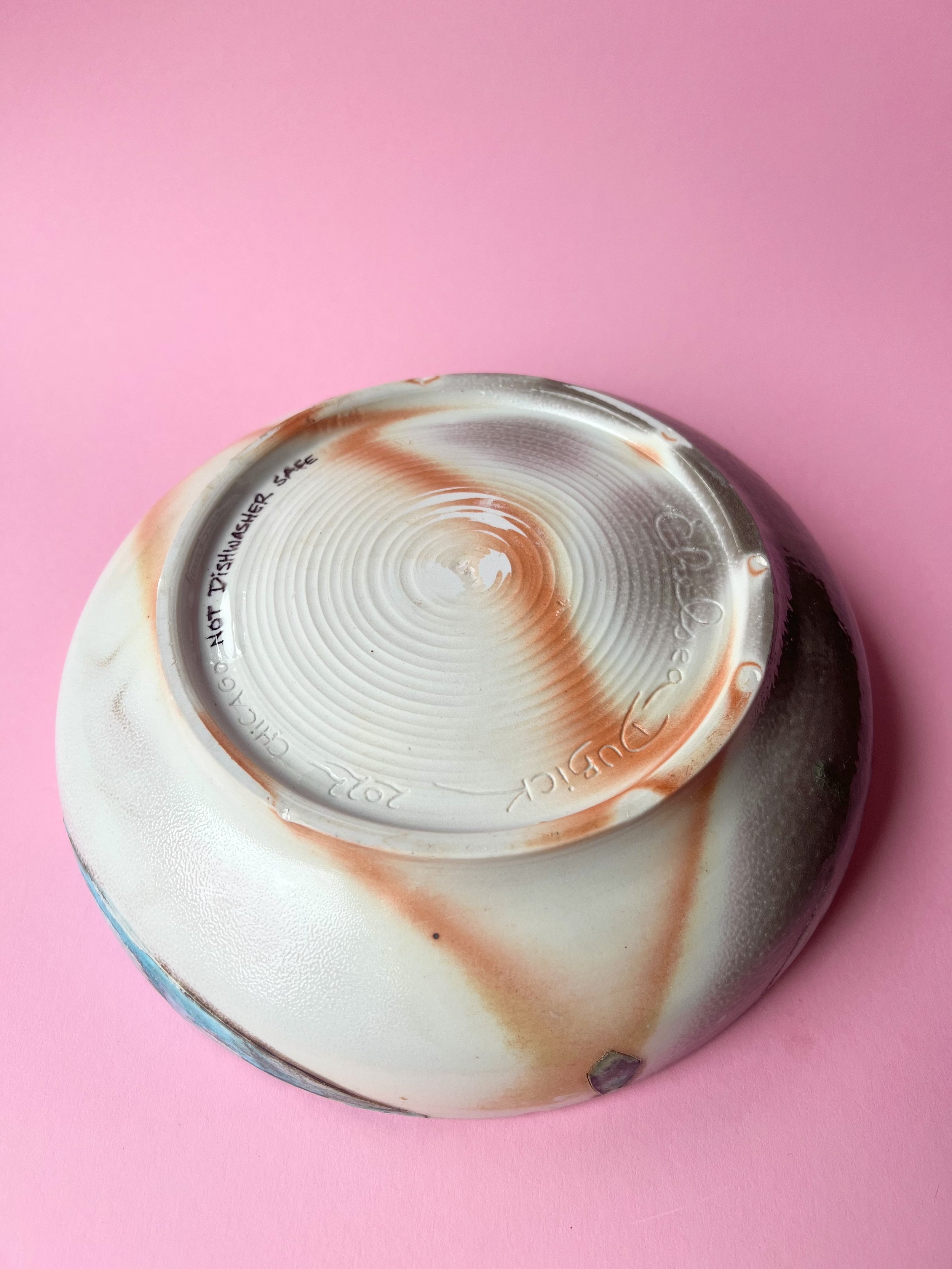
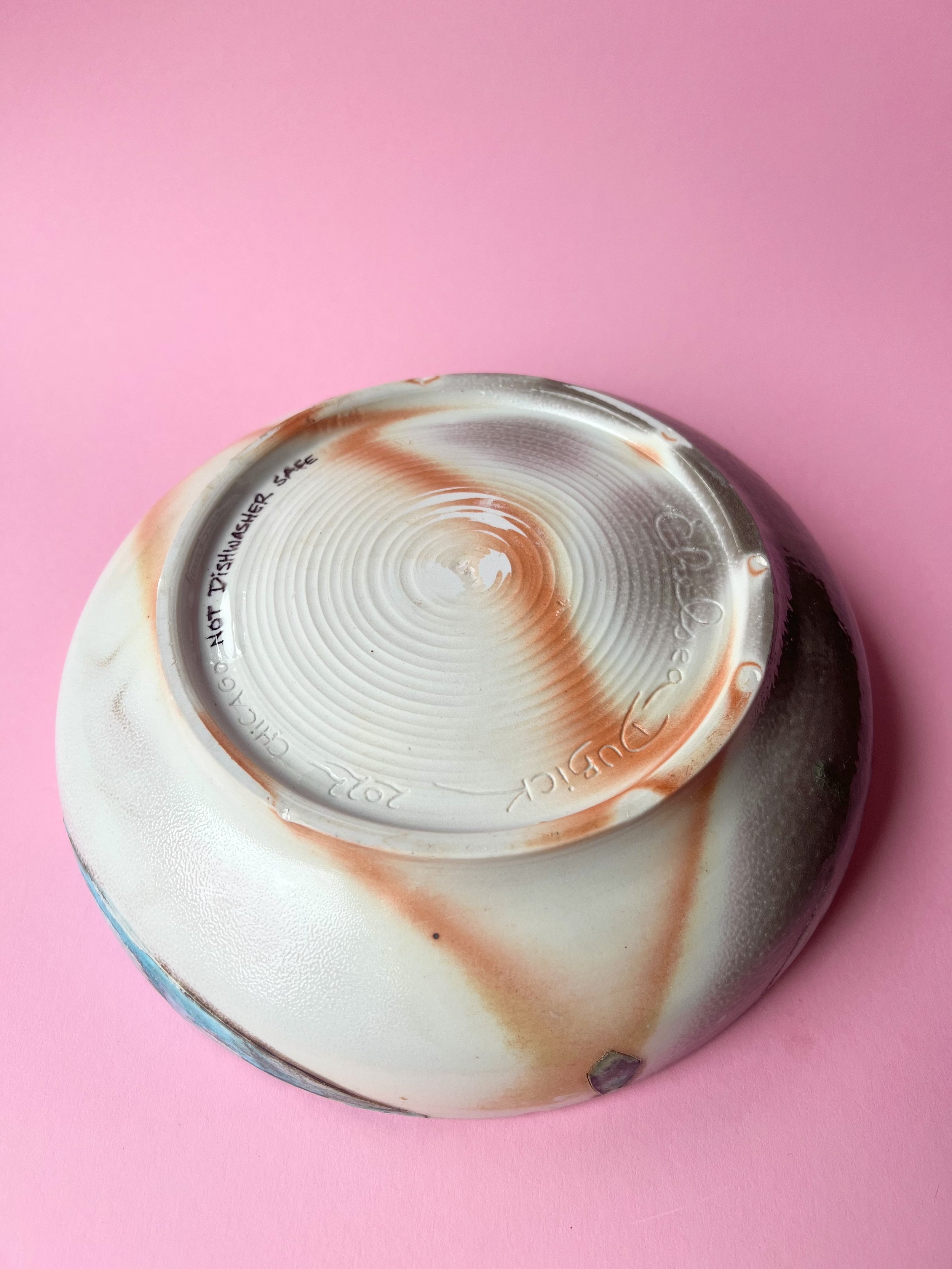
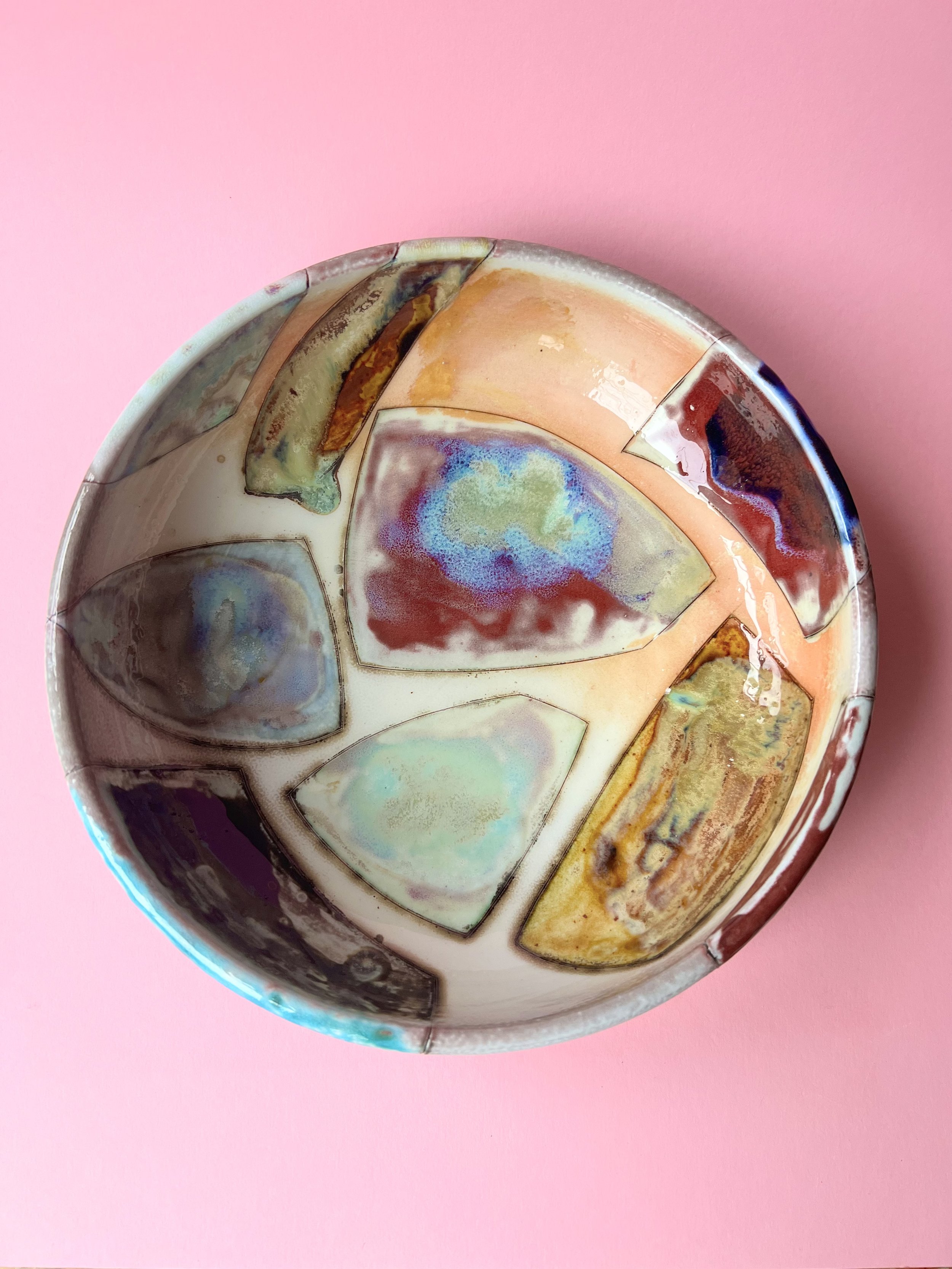
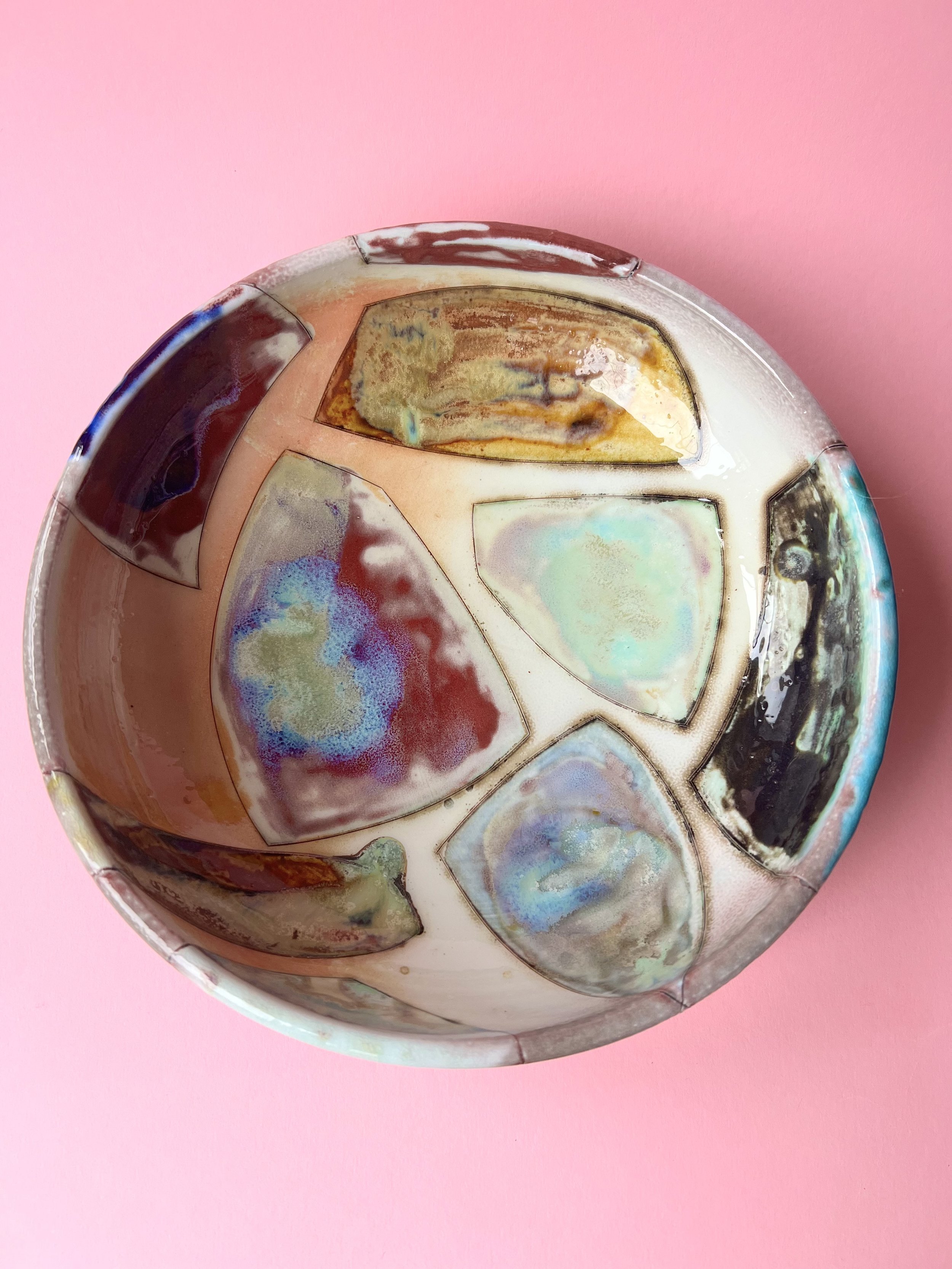
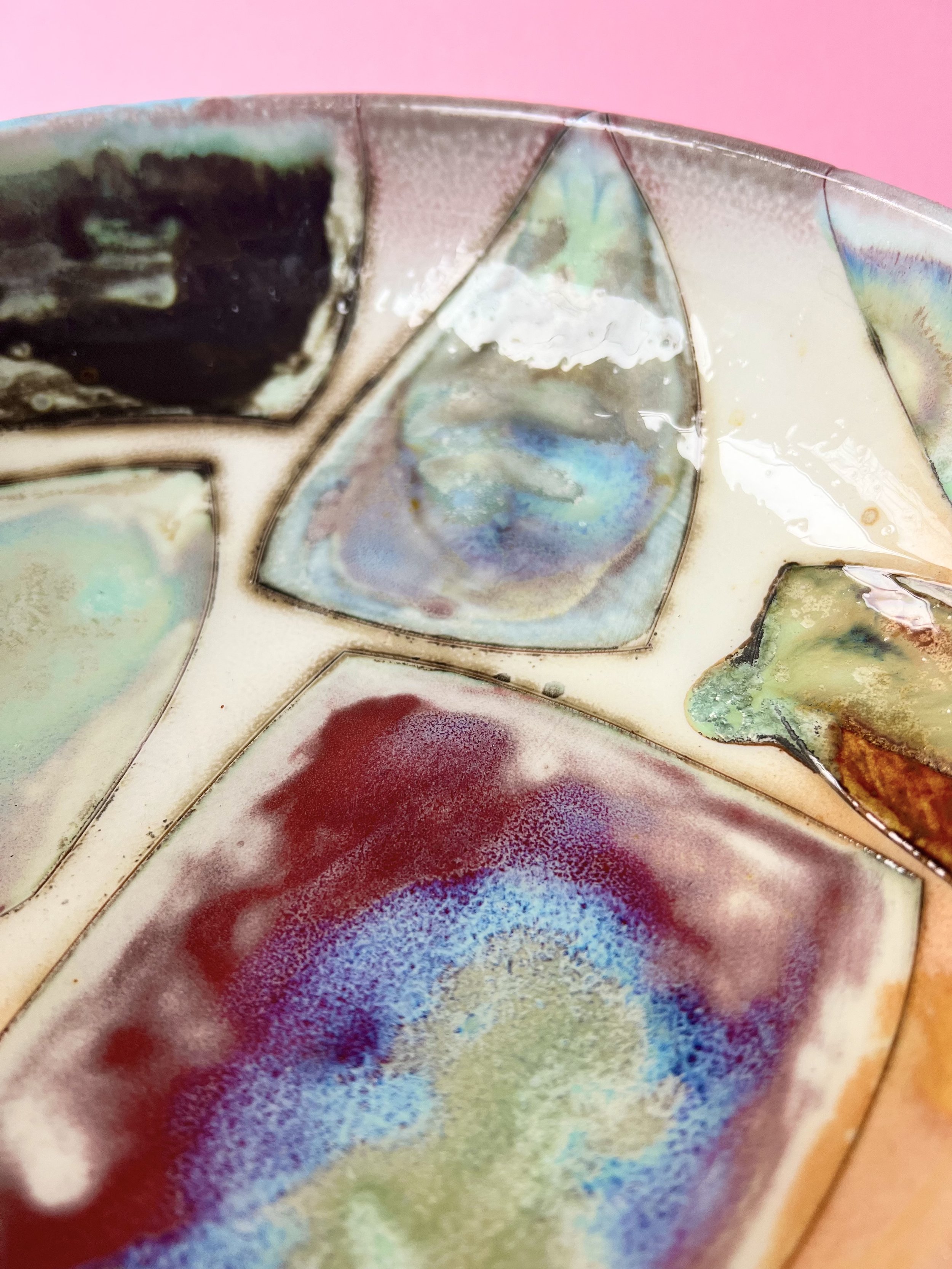
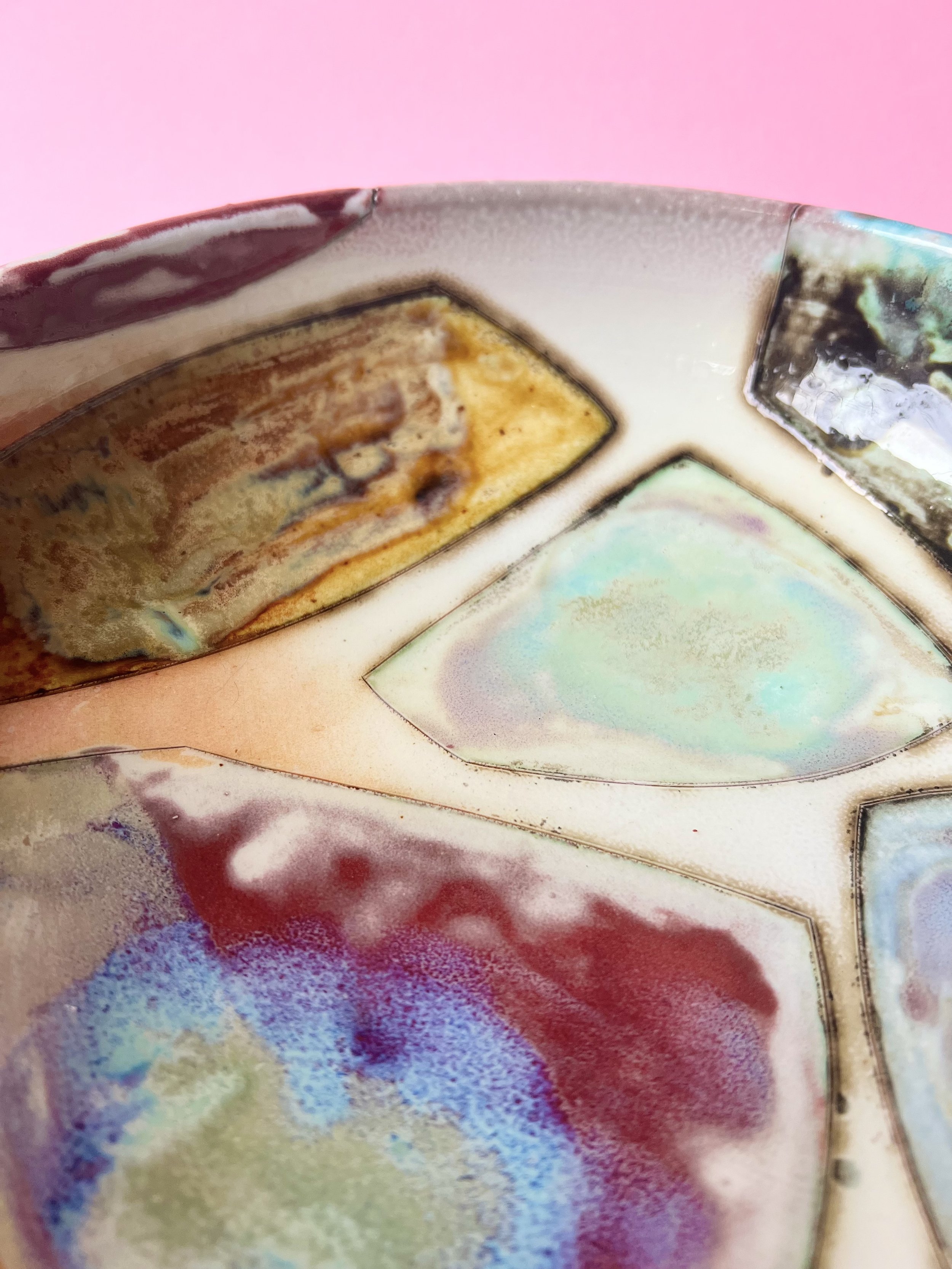
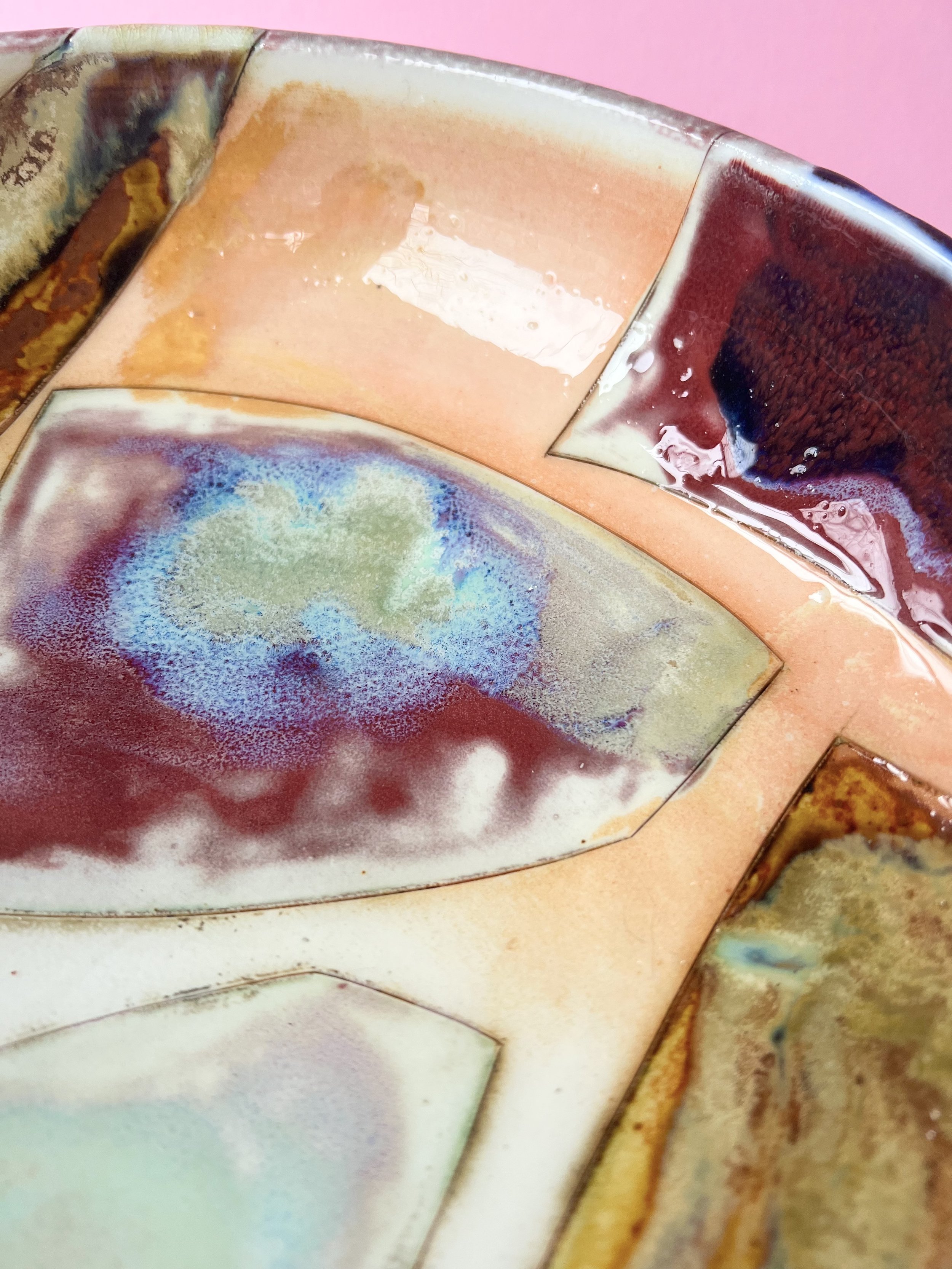
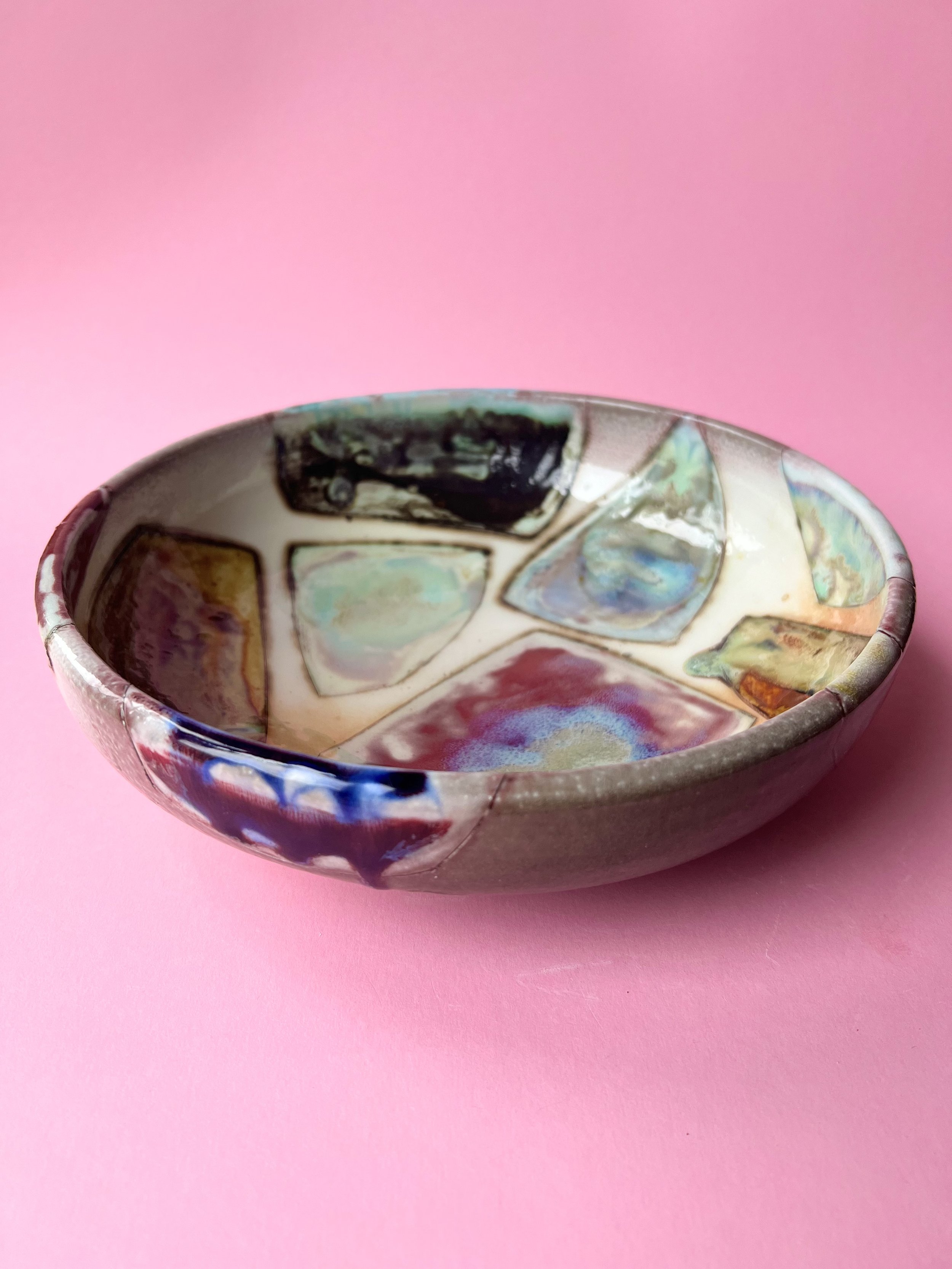
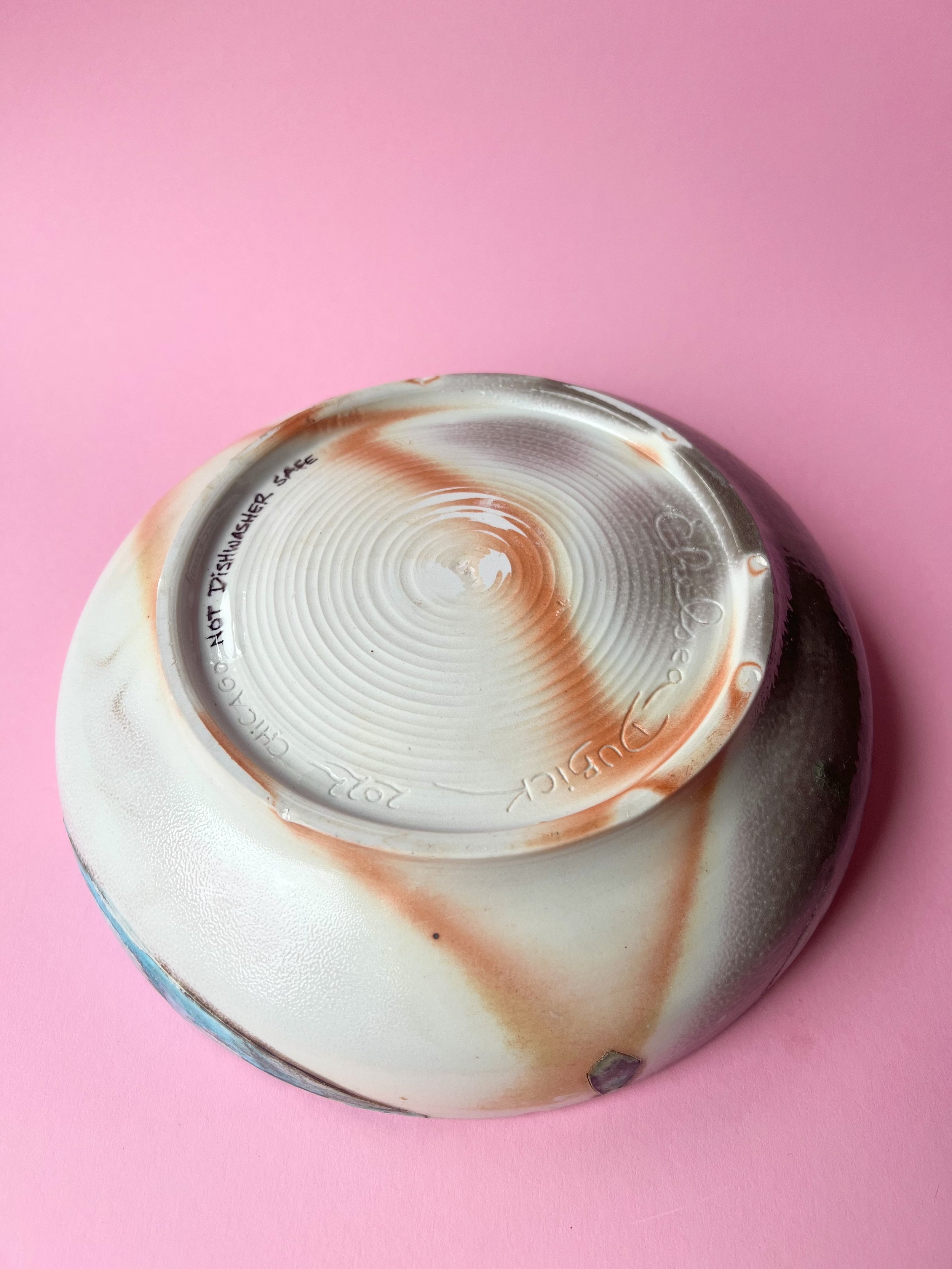
Bowl: Soda Geometry (Large)
This bowl is a gorgeous experiment in glaze, geometry and soda firing. Impossible to replicate and oh so delicious.
The inside of the bowl was coated in resin to create a smoother surface after the soda firing. Food safe but not dishwasher safe.
Can be used as. a functional piece or hung on the wall.
Each soda fired piece is one-of-a-kind as atmospheric firings are unpredictable and can yield stunning results. Soda firing takes an enormous amount of time, energy, labor and resources and is usually a community effort. In the soda firing process, soda ash (sodium carbonate) is added to the kiln at cone 9 (2300°) and the sodium vapor combines with silica in clay to form sodium-silicate glaze. The soda also interacts with the slips and glazes to create swirling unpredictable colors that shift and change around the piece. The marks on the bottom are from the wadding used to hold the piece up off the kiln shelf so that glaze drips won’t fuse it to the shelf. They can leave lovely flame marks and are a telltale sign a piece is soda fired, though they don’t always happen, especially in low soda areas of the kiln.
This bowl is a gorgeous experiment in glaze, geometry and soda firing. Impossible to replicate and oh so delicious.
The inside of the bowl was coated in resin to create a smoother surface after the soda firing. Food safe but not dishwasher safe.
Can be used as. a functional piece or hung on the wall.
Each soda fired piece is one-of-a-kind as atmospheric firings are unpredictable and can yield stunning results. Soda firing takes an enormous amount of time, energy, labor and resources and is usually a community effort. In the soda firing process, soda ash (sodium carbonate) is added to the kiln at cone 9 (2300°) and the sodium vapor combines with silica in clay to form sodium-silicate glaze. The soda also interacts with the slips and glazes to create swirling unpredictable colors that shift and change around the piece. The marks on the bottom are from the wadding used to hold the piece up off the kiln shelf so that glaze drips won’t fuse it to the shelf. They can leave lovely flame marks and are a telltale sign a piece is soda fired, though they don’t always happen, especially in low soda areas of the kiln.
This bowl is a gorgeous experiment in glaze, geometry and soda firing. Impossible to replicate and oh so delicious.
The inside of the bowl was coated in resin to create a smoother surface after the soda firing. Food safe but not dishwasher safe.
Can be used as. a functional piece or hung on the wall.
Each soda fired piece is one-of-a-kind as atmospheric firings are unpredictable and can yield stunning results. Soda firing takes an enormous amount of time, energy, labor and resources and is usually a community effort. In the soda firing process, soda ash (sodium carbonate) is added to the kiln at cone 9 (2300°) and the sodium vapor combines with silica in clay to form sodium-silicate glaze. The soda also interacts with the slips and glazes to create swirling unpredictable colors that shift and change around the piece. The marks on the bottom are from the wadding used to hold the piece up off the kiln shelf so that glaze drips won’t fuse it to the shelf. They can leave lovely flame marks and are a telltale sign a piece is soda fired, though they don’t always happen, especially in low soda areas of the kiln.